|

|
|
根据国内脱硫废水零排放的发展现状, 相对于传统的蒸汽蒸发技术, 烟气利用技术由于利用烟气余热蒸发脱硫废水, 节省能耗, 系统工艺简单, 节约占地, 已越来越受到关注。分析研究大型燃煤电厂脱硫废水利用旁路烟道喷雾干燥、烟道直喷干燥、烟气余热蒸发3种技术, 通过计算和分析每种技术的特点, 对各自优缺点做出客观的分析, 为后续脱硫废水零排放项目中烟气利用技术的实施提供参考。
近年来, 国家对燃煤电厂产生的水环境影响提出了更高的要求———实现全厂废水零排放, 以期达到良好的环境效益和社会效益。燃煤电厂废水回收基本上是经过全厂水务管理及梯级利用后回用至脱硫用水, 因此如何处理脱硫系统产生的高含盐量废水是全厂废水零排放的关键。
1 脱硫废水零排放现状
1.1 脱硫废水水质特点
目前燃煤电厂主要采用石灰石—石膏湿法烟气脱硫工艺。该工艺中脱硫循环浆液由于不断吸收来自烟气及石灰石中的氯化物, 导致氯离子浓度不断增高, 其浓度的增高会带来诸多不利影响, 如:抑制石灰石的溶解, 使浆液的p H值降低, 影响二氧化硫的吸收效果, 使硫酸钙 (CaSO4) 易于结垢, 还易导致金属材料的腐蚀等。此外, 氯离子浓度过高也会影响脱硫副产物石膏的品质。为保证脱硫系统的正常运行, 一般应控制吸收塔中氯离子含量低于20000mg/L。另外, 与氯离子一样, 粉尘也会在循环浆液中不断积累, 脱硫系统的微细粉尘主要来自烟气中携带的粉尘、石灰石中的惰性物质、停止生长的小石膏晶体及工艺水中的杂质等。为保证商用石膏的纯度和系统浆液正常的物理化学性质, 需要对系统内的微细粉尘浓度进行控制。
因此, 为了保证脱硫系统的正常运行和脱硫副产物石膏的品质, 必须排放一定量的脱硫废水。脱硫废水水量、水质受煤质和脱硫系统工艺用水的水质影响很大, 且水质和水量随上述影响因素的变化而出现较大变化, 基本上是一厂一水量、水质。
1.2 国内脱硫废水零排放现状
根据调研, 目前国内已实施脱硫废水零排放的发电厂共有23家, 处理水量0.5~47 t/h, 其中, 目前已建成并且正式投运的大型燃煤电厂脱硫废水项目情况如表1所示。
相对于传统的蒸汽蒸发技术, 烟气利用技术由于利用了烟气余热蒸发脱硫废水, 系统简单, 节约占地, 已越来越受到关注。
2 脱硫废水烟气利用技术
烟气利用技术主要有旁路烟道喷雾干燥、烟道直接喷雾干燥、烟气余热浓缩蒸发等方法, 其与机组烟气系统热平衡和各工艺段参数密切相关, 以下分析这3种烟气利用的详细工艺特点。
2.1 旁路烟道喷雾干燥工艺
该工艺原理是从脱硝系统出口引出热烟气, 经旁路烟道送至喷雾干燥塔;脱硫废水经管路进入干燥塔, 经过高速旋转的雾化器雾化为细小液滴群后与烟气进行充分的热交换, 利用烟气余热瞬间干燥脱硫废水, 蒸发产生的大部分固体物质从喷雾干燥塔底部的排放口排出;经喷雾干燥塔干燥后的尾气返回电除尘器进口。该工艺流程如图1所示。
蒸发废水需要的能量计算公式为:
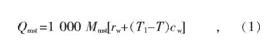
式中:Mmst为需蒸发废水的质量;T为环境温度;T1为蒸发后蒸汽温度;rw为水的汽化潜热, 取2262kJ/kg;cw为水的比热容, 4.187kJ/ (kg˙℃) 。废水温度T取25℃, 蒸汽温度T1取125℃, 可得干化1t废水所耗能量为3.11×106 kJ。
由于脱硝出口烟气原用于加热进入空预器的冷风, 以回收热量, 用于废水干燥后会造成热量损失, 空预器传热效率按95%计, 干燥1 t废水所耗热量折合标煤100.8 kg, 按标煤价900元/t计, 干燥1 t废水消耗的热量折算费用约90.7元。
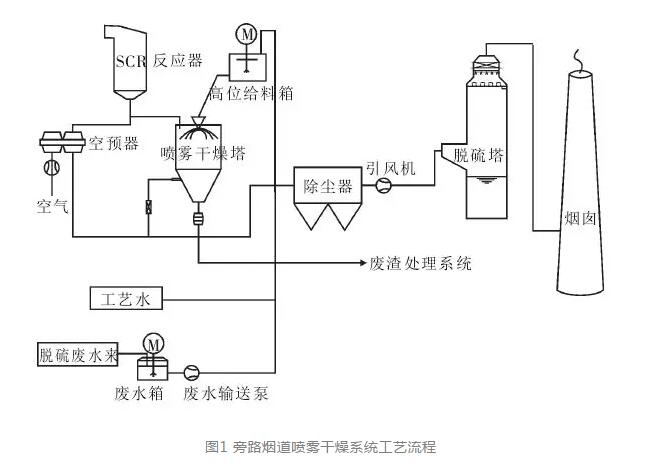
因此全厂脱硫废水量较大时, 可考虑先将脱硫废水浓缩减量后再进入旁路烟道喷雾干燥, 以降低整套系统的能耗。
脱硝出口烟气约为350℃, 干燥废水后降至约125℃, 烟气焓降约200kJ/kg, 经计算, 干燥1 t废水所需烟气量约为15550kg, 采用此工艺的各类型机组干燥脱硫废水所需烟气质量和占总烟气的比值见表2 (单台机组) 。
从表2可以看出, 理想状态下300MW, 600MW和1000MW机组单台脱硫废水量分别为4t/h, 7t/h和12t/h。各类型机组 (单台机组) 干燥脱硫废水所需的烟气占总烟气量比值均接近5%。机组额定负荷时, 从脱硝出口抽取约5%的烟气会有空预器硫酸氢氨结露区跨层的风险。如采用该工艺, 需要对空预器进行改造, 增加镀搪瓷段的长度。当机组处于50%THA (机组热耗保证工况) 负荷以下运行时, 旁路烟气量会相应减少, 干燥塔中流场被破坏而导致废水接触干燥塔表面引起结垢、腐蚀, 所以机组低于50%THA负荷运行时该系统需停运。而机组实际脱硫废水量超过理想值, 干燥脱硫废水所需的烟气比例超过5%, 则需要经过浓缩再进行旁路烟气干燥。
该工艺可将废水蒸干物混入粉煤灰中。参照典型脱硫废水水质表, 氯离子浓度按15000mg/L, 飞灰含量按18g/m3计, 计算结果如表3所示 (单台机组) 。
由表3可知, 最终混入飞灰中的氯离子含量均达到0.3%以上。根据GB 175-2007《通用硅酸盐水泥》第7.1条规定, 水泥中氯离子含量不大于0.06%, 且水泥中粉煤灰占比约20%~40%, 所以机组使用该工艺后, 其粉煤灰不宜用于制作硅酸盐水泥。但JC/T 409-2001《硅酸盐建筑制品用粉煤灰》中对用于加气混凝土、粉煤灰砖、砌块、粉煤灰蒸养陶粒及掺加粉煤灰的建筑板材等硅酸盐建筑制品用的粉煤灰无氯离子含量要求, 所以使用该工艺后, 机组的粉煤灰仍可用于生产以上建筑制品。
该工艺的优点是系统热量利用率高, 热损失小;工艺简单, 设备少, 喷雾干燥塔一般布置在靠近空预器的位置, 占地比较小。
2.2 烟道直接喷雾干燥工艺
烟道直喷干燥工艺是将脱硫废水直接通过雾化喷入空预器后、电除尘器前烟道内, 废水中水分蒸发后被烟气携带至脱硫塔, 废水晶体被电除尘器捕捉脱除。该工艺具有系统简单、投资成本和运行费用低、对场地要求低等优点。
根据式 (1) 计算可得, 干化1t废水所耗能量为3.06×106 kJ。各类型机组干燥脱硫废水所需烟气质量和占总烟气的比值见表4 (单台机组) 。
表4 各类型机组干燥脱硫废水所需烟气质量和占总烟气的比值 (单台机组)
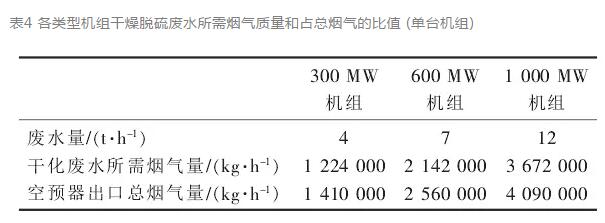
由表4可知, 根据理想状态下单台机组废水量, 空预器出口的总烟气量略大于干燥废水所需的烟气量, 理论上如果烟气和废水充分接触, 可以实现对废水的干燥。但由于空预器后烟气温度仅125℃, 废水喷入烟道后蒸发速度较慢, 所以必须保证废水与烟气有充分的接触时间。如果烟道距离不够长且回转式空预器出口烟气流场不均匀, 会出现局部废水无法和烟气充分接触的情况, 可能会有部分废水无法在进入电除尘器前被干化。
该工艺烟气干燥废水后的蒸干物将混入粉煤灰中, 与上节所述旁路烟气喷雾干燥工艺的粉煤灰情况基本相同。
如机组采用低低温电除尘器, 空预器至烟气冷却器之间的烟道较短, 可能会导致未干燥的废水进入烟气冷却器, 易使烟气冷却器发生积灰、结垢造成堵塞;如果未干燥的废水进入电除尘器, 还会导致电除尘极板腐蚀。因此, 设置低低温电除尘器的机组不推荐采用烟道直接喷雾干燥技术。
2.3 烟气余热浓缩蒸发
该工艺是利用部分电除尘器与脱硫塔之间的烟气, 将废水在浓缩塔内喷淋, 与烟气接触后蒸发, 未蒸发的部分通过泵循环进入浓缩塔加热, 脱硫废水在烟气的加热下不断浓缩, 其中的溶解物逐步达到饱和并析出, 析出的物质通过板框压滤机压制成泥饼后外运处理。工艺流程见图2。
根据式 (1) 计算可得, 干燥1t废水所耗能量为2.90×106 kJ, 由于所用烟气热量为电除尘器后的废热, 所以该热量不产生费用。电除尘器出口烟气约为90℃, 浓缩废水后降至约55℃, 烟气焓降约35kJ/kg, 经计算, 采用此工艺的各类型机组干燥脱硫废水所需烟气量和水份含量见表5 (单台机组) 。
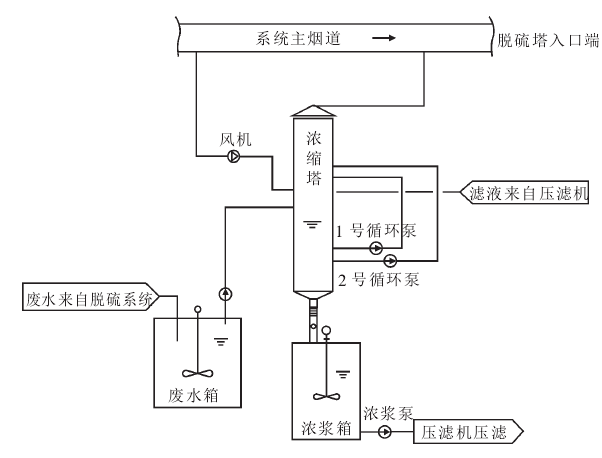
图2 烟道余热浓缩蒸发系统工艺流程
由表5可知, 理想状态下抽取约30%电除尘器后的烟气量就可以蒸发全部废水和工艺水, 并且烟气中的水分未达到饱和, 可以实现对全部废水的蒸发。实际运行中废水量超过理想值是否能够完全蒸发还需经过中试检验。
烟气蒸发废水后热量减少, 会减少脱硫系统的蒸发量, 这将破坏脱硫系统原有的水平衡。由于不同地区的煤种和脱硫系统工艺用水水质不同, 压滤后的泥饼性质需要经过鉴定。
该工艺的优点是利用了难以利用的废热, 直接运行费用低;工艺简单, 设备少, 维护量小;废水无需进行预处理及软化, 可直接进入该系统进行浓缩。
3 结语
针对大型燃煤电厂脱硫废水采用旁路烟道喷雾干燥、烟道直喷干燥、烟气余热蒸发3种技术进行研究分析, 认为其共同优点是利用烟气热量, 热损失小, 工艺简单设备少, 运行维护量小, 占地少, 且3种烟气利用技术都对处理废水量有一定的限制。旁路烟道喷雾干燥和烟道直喷干燥方法干燥物都混入粉煤灰中综合利用, 而烟气余热蒸发的干燥物混入泥饼中需外运处理。
由于烟气利用技术受机组烟气系统热量平衡及脱硫系统水平衡的影响, 在后续具体实施过程中需结合项目烟气系统和实际废水量具体核算选择方案。烟气蒸发后的干燥物混入粉煤灰对粉煤灰品质造成的影响需要结合项目当地灰渣综合利用情况具体分析决策。
- 西安热工研究院有限公司
- 中国电机工程学会
- 国家核电技术公司
- 中国电力科学研究院
- 火力发电分会(电机工程学会)
- 火力发电分会(中电联)
- 中国电力规划设计协会
- 中国电力建设企业协会
- 华润电力控股有限公司
- 国电电力发展股份有限公司
- 华能国际电力股份有限公司
- 大唐国际发电股份有限公司
- 中国华电工程(集团)有限公司
- 山东黄台火力发电厂
- 中国华电集团发电运营有限公司
- 内蒙古蒙电华能热电股份有限公司
- 园通火力发电有限公司
- 广西柳州发电有限责任公司
- 株洲华银火力发电有限公司
- 内蒙古岱海发电有限责任公司
- 山西漳山发电有限责任公司
- 湖北华电黄石发电股份有限公司
- 黑龙江华电佳木斯发电有限公司
- 陕西蒲城发电有限责任公司
- 福建华电永安发电有限公司
- 开封火力发电厂
- 华电国际邹县火力发电厂
- 中山火力发电有限公司
- 山西阳光发电有限责任公司
- 国电长源电力股份有限公司
- 山东新能泰山发电股份有限公司
- 宜昌东阳光火力发电有限公司
- 扬州火力发电有限公司
- 太仓港协鑫发电有限公司
- 甘肃电投张掖发电有限责任公司
- 陕西渭河发电有限公司
- 国投钦州发电有限公司
- 大唐淮南洛河发电厂
- 国电丰城发电有限公司
- 靖远第二发电有限公司
- 国华绥中发电有限公司
- 元宝山发电有限责任公司
- 开封火力发电厂
- 云南华电巡检司发电有限公司
- 云南华电昆明发电有限公司
- 国投宣城发电有限责任公司
- 山东黄岛发电厂
- 国投北部湾发电有限公司
- 西北发电集团
版权所有©火力发电网 运营:北京大成风华信息咨询有限公司 京ICP备13033476号-1 京公网安备 110105012478 本网站未经授权禁止复制转载使用